Can I Put My Cable Box in a Cabinet? A Mornington Homeowner’s Guide to Setup, Safety & Signal Strength
Can I Put My Cable Box in a Cabinet? A Mornington Homeowner’s Guide to Setup, Safety & Signal Strength
If you’re setting up a clean and clutter-free entertainment area in Mornington, Australia, the idea of hiding devices like your cable box inside a cabinet may feel like a no-brainer. But before you start tucking that box out of sight, it’s important to understand how placement affects performance, signal strength, ventilation, and even remote functionality.
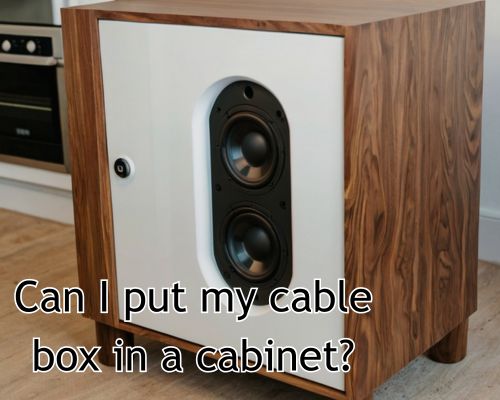
So, can you put your cable box in a cabinet? The short answer is yes, but with conditions. With Leona Rodriguesi of Mornington Cabinet Makers, we’ll explore the ins and outs of placing a cable box in a cabinet, the key technical and functional considerations, and some smart workarounds—all optimized for Mornington homes.
📺 Why People in Mornington Are Hiding Their Cable Boxes
A growing number of Mornington Peninsula homeowners are upgrading their living spaces with custom cabinetry, wall-mounted TVs, and minimalist home theatres. As a result, bulky media gear like cable boxes often clash with the aesthetic.
Here are some local trends influencing this:
- Coastal-style cabinetry is popular in Mornington homes, featuring clean lines and concealed storage.
- TV wall units with integrated PVC or MDF cabinets are in high demand.
- Increasing local interest in wireless and smart home solutions, like those available through regional AV specialists in Mount Eliza or Frankston.
All of this creates a desire to hide away unsightly gadgets—including cable boxes—without sacrificing functionality.
🛠️ Can You Put a Cable Box in a Cabinet? Yes, But Consider These 5 Factors
1. Remote Control Signal (Infrared Limitations)
Most cable boxes use IR (infrared) signals, which do not travel through solid materials like wood or metal.
🔧 Solution: Use an IR repeater/extender. These small devices pick up the remote’s signal outside the cabinet and relay it to your cable box inside.
Alternatively, look for RF (radio frequency) remote controls or Bluetooth-enabled boxes, which can work through cabinetry.
2. Ventilation and Heat Build-Up
Cable boxes generate heat, and trapping that heat in a sealed cabinet can lead to overheating, shortened device lifespan, or performance issues.
🔧 Solution: Ensure the cabinet has ventilation holes at the back or sides, or opt for cabinets with mesh or slatted panels for passive airflow. You can also install low-noise cabinet cooling fans, widely available from tech stores in Mornington or Dandenong.
3. Wi-Fi and Signal Interference
If your cable box connects to the internet via Wi-Fi (common with streaming-enabled models like Foxtel iQ5), placing it in a cabinet may impact signal strength, especially if it’s far from the router.
🔧 Solution: Consider ethernet cabling through the cabinet or use a Wi-Fi extender to boost the signal strength inside your entertainment unit.
4. Cable Management
Routing HDMI, power, and antenna cables into and out of the cabinet requires careful planning.
🔧 Solution: Choose TV units with rear access panels and pre-drilled cable ports. Local Mornington furniture makers often offer custom cabinetry that accommodates cable pathways seamlessly.
5. Aesthetic vs. Accessibility Trade-Off
While it’s tempting to completely hide your cable box, consider how often you need to access it—whether for restarts, updates, or physical buttons.
🔧 Solution: Use front-access cabinets with glass doors, which maintain line-of-sight for IR remotes while keeping visual clutter minimal.
🧠 Pro Tips from AV Experts in Mornington
We spoke to local installers and AV enthusiasts across Mornington, Mount Martha, and Somerville, and they emphasized a few critical tips:
- Use smart universal remotes like Logitech Harmony to consolidate device controls—even from inside cabinets.
- Don’t stack cable boxes with other hot-running devices like AV receivers—this magnifies heat issues.
- If your cabinet is fully enclosed, add a cooling fan with thermal sensors. These can auto-activate when temperatures rise.
Some even suggested repositioning the cable box to an adjacent hallway closet or laundry shelf and running cables through the wall—an approach that combines performance with a clean look.
🏡 Cabinet-Friendly Tech Options for Mornington Homes
If you’re renovating or designing your entertainment setup, look for tech that’s designed to live inside cabinets:
1. Cable Boxes with RF or Bluetooth Remotes
Many new models from providers like Foxtel or Fetch TV offer RF remotes, which don’t require line-of-sight.
2. HDBaseT or HDMI-over-Ethernet Extenders
These allow you to place your cable box in a different room and still connect to your TV with no signal loss—perfect for modern open-plan homes in Benton Square or Mornington Heights.
3. Smart Streaming Replacements
Consider replacing your traditional cable box with a streaming stick like Apple TV, Google Chromecast, or Amazon Fire Stick. These are compact, generate less heat, and are designed to work with Wi-Fi, often from inside cabinets or behind TVs.
🛒 Where to Buy IR Repeaters and AV Cabinet Accessories in Mornington
Need local options? You can find helpful gear at:
- The Good Guys – Mornington (for IR repeaters and universal remotes)
- JB Hi-Fi Frankston (for smart TV accessories and Wi-Fi extenders)
- Bunnings Warehouse (for cabinet cooling fans and cable clips)
- Harvey Norman – Mornington (custom media cabinets with AV features)
Local custom cabinetry experts like Mornington Cabinet Makers or Peninsula Cabinets can even design solutions specifically for your space.
✅ Summary: Should You Put Your Cable Box in a Cabinet?
Here’s a quick decision matrix for Mornington residents:
Question | Answer |
---|---|
Is your remote IR-only? | Use an extender or RF/Bluetooth model |
Is the cabinet enclosed? | Add ventilation or cooling |
Are you using Wi-Fi? | Ensure signal strength or use ethernet |
Want a sleek look? | Use glass-front or slatted cabinets |
Streaming-only household? | Consider ditching the cable box altogether |
📦 Final Word: Function Meets Style in Mornington Living Rooms
So yes—you can put your cable box in a cabinet. But in Mornington’s coastal climate, with our focus on home aesthetics, smart tech, and durability, it’s worth planning the setup carefully.
With the right accessories, smart tech upgrades, and local help, you can declutter your entertainment zone without sacrificing usability. Whether you’re watching the footy on Channel 7, streaming Stan, or binging on Netflix, your cabinet setup should enhance your experience—not block it.
Want help setting up the perfect cabinet for your media gear in Mornington? Reach out to a local AV technician or cabinetmaker (see Mornington Cabinet Makers) and make your entertainment space both smart and stylish.